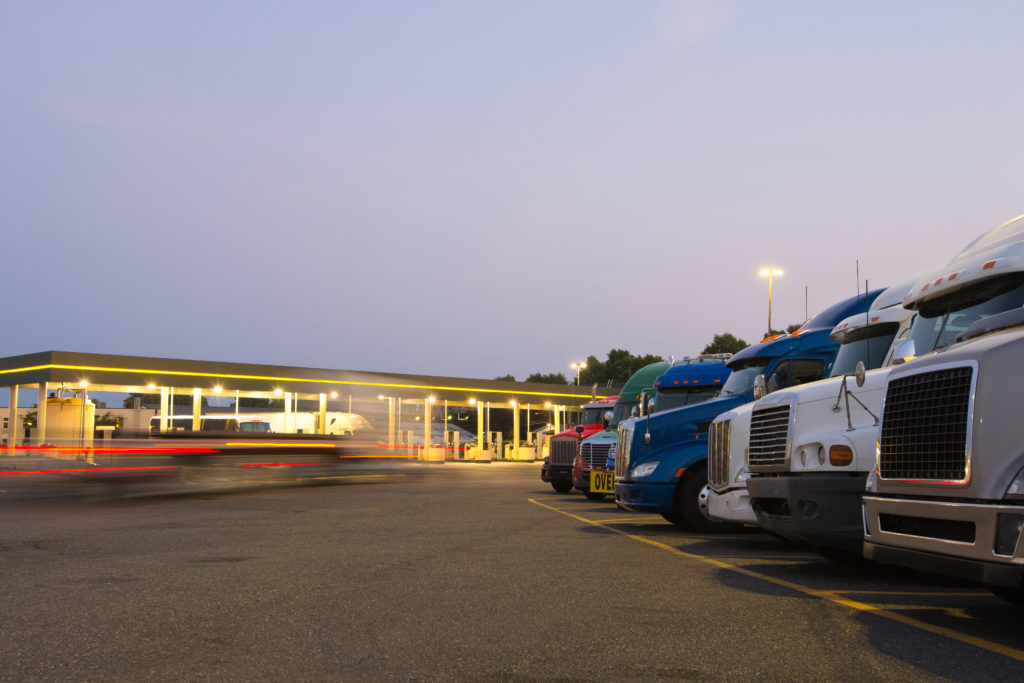
At the recent 2020 American Trucking Associations Technology and Maintenance Council Annual Meeting in Atlanta, Airman Products unveiled its new Automated Landing Gear Deployment and Retraction Technology.
The company’s patent-pending device allows drivers to limit their exposure to potential injuries–such as knee and back damage–by eliminating manual cranking needs for raising and lowering the landing gear of a truck, and replacing it with the flip of a switch.
“What we’re bringing to the fleets is a faster solution that requires significantly less effort out of the driver,” said vice president of Airman sales, Jim Babbitt.
The electrically-driven unit can be OEM-installed in under an hour, works easily with all existing landing gear makes and models, and only weighs 15 pounds. A driver can deploy and retract landing gear much more quickly with the new technology than he or she could manually.
When drivers work with the manual system and sustain injuries, they often end up missing work for months–which can even cost them their jobs.
“You do this tens of thousands of times over a lifetime of being a truck driver, and that’s going to cause problems,” said Shane LaHousse, Airman vice president of engineering. “Automation is the way to eliminate this problem”
Repetitive cranking motion can also because heavy wear on muscles and joints, especially in aging drivers, which is a growing issue as the median truck driver age continues to rise.
“Depending on the equipment and circumstances, it can take between 50 to 60 crank arm rotations to get the legs on a trailer’s landing gear at the ground, and this task can keep some otherwise great drivers from working or coming back to work,” LaHousse explained. “Operating the crank arm can be awkward and physically taxing, even if the driver is young and uses the proper technique for landing gear operation, so we’ve taken this task out of the driver equation by automating it.”
Babbitt assures that this is a major solution.
“The fleets we’ve surveyed tell us that shoulder, back, and rotator cuff injuries are at the top of their list for workers’ comp claims, and that cranking landing gear up and down can cause or exacerbate these injuries,” said Babbitt. “Truck driving is already a physically demanding profession, so our automated system focuses on one primary stressor–making trailer drops and hookup operations safer and faster, while improving the truck driver experience and, as a result, driver retention.”
According to LaHouse, the Automated Landing Gear Deployment and Retraction system also increases lot utilization by allowing trailers to park closer together. This is made possible because the controller is mounted directly under the trailer apron and there is no longer a need to be able to reach a crank arm.
Babbitt said installing the system is simple–it arrives in kit form with all mounting hardware included. It only needs two bolts on the landing gear crossbar removed, the Airman landing gear actuator attached, and then the crossbar reinstalled.
The interface also only needs a 12-volt power supply, and the unit’s control box mounts easily under the trailer. Its two-way toggle switch sits on the side of the trailer frame rail and is easily accessible.
There is no maintenance required once installed, besides periodic battery replacement as needed. The company’s landing gear actuator is self-contained and does not need any lubrication.
“Some landing gear manufacturers offer automated systems now, but they are expensive, upgrading requires discarding an existing drive leg, and if the landing gear is damaged, may require complete replacement,” said Babbitt. “Not only is the Airman system about half the cost of other systems, it also works universally with all existing landing gear makes and models, and doesn’t have to be replaced if the landing gear is damaged.”
Airman also asserts that fleets with multiple trailer brands using various types of landing gear are now able to use one piece of equipment and one single source overall. Thus, whether a fleet orders the Airman Automated Landing Gear Deployment and Retraction Technology on new trailers, retrofits older trailers, or utilizes both options, it can still increase its parts inventory by just one SKU.
As of now, implementing the new automated landing gear system–which is expected to enter production in the third quarter–will only cost fleets about $700 per unit.
Additionally, it will come with a standard five-year warranty, or a seven-year warranty with a fleet agreement.
Reader Interactions