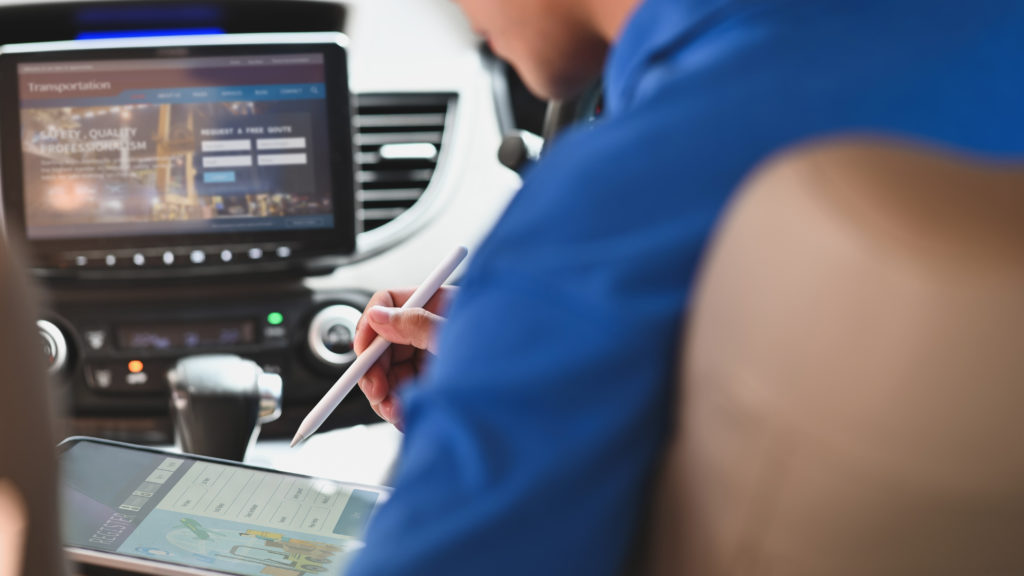
All carriers across the trucking industry have been forced to adapt quickly to the major changes brought on by COVID-19, and one major aspect of these new changes has become investments into technology.
Monitoring employee health, improving loading and delivery efforts to avoid human contact, or just transitioning industry workers to working from home have all brought new technological methods and programs to trucking companies, and industry experts say these changes are boosting overall efficiency and effectiveness that will become a regular part of the trucking industry as a whole.
For example, alcoholic beverage distributor Southern Glazer’s Wine & Spirits has implemented a text message system that requests a health form completion from drivers and employees two hours before their shifts begin. Throughout the pandemic, this method has become a vital communication tool as the company uses this same system to send important information to employees as it can reach them quickly, even when they are working remotely or on the road.
Telematics system and electronic logging device data have also increased heavily during this time, and fleets are learning how to implement these systems into their daily routines to boost operation quality and efficiency.
“We are able to tell our customers our projected delivery time from the first stop to the last, with added traffic and weather impacts,” said McLane Co. director of transportation support, Jim VonAchen. “Our customers can then prepare for our arrival 12 hours out and make sure they have resources ready.”
VonAchen explained that these changes allowed McLane to update all of its delivery network procedures in order to reduce costs and meet rising demands when the pandemic began.
“As you scale up from a small company, these tools become invaluable,” he explained.
“We don’t see an end in sight to this any time soon,” agreed Ron Flanary, senior vice president of national operations for Southern Glazer’s. “We are making the investment in technology,” which will be vital for the company’s fleet of 2,189 straight trucks, 721 tractors, and 2,500 drivers.
Fleet Advantage chief operating officer, Jim Griffin, notes that many carriers are now kicking themselves for not having invested in advanced trucking equipment before COVID-19 hit.
“We have some clients that had put off fleet modification and felt that was a mistake,” Griffin said. “They should have been more prepared.” This is especially true as more fleets have been left with aging equipment throughout the pandemic, which hinders companies from having cost-reducing automated safety systems and improved fuel efficiency.
Older trucks will be replaced quickly with newer, advanced models as soon as the economy bounces back, and growth will continue, Griffin predicts.
Technology has also made remote jobs much easier during stay-at-home orders, and there have been more opportunities than ever to secure this kind of work. Additionally, many trucking companies have found that remote scheduling and digital management practices through a decentralized business model have also helped employees working in-office.
“You never thought you could send people home for a long period and keep the national supply chain to grocery stores holding up very well,” said Flanary of his surprise at the efficiency of these methods.
For Clean Harbors, the company shifted into a nearly-fully remote work and dispatch system within only eight days, which included the time it took to feel things out and solve initial problems with the transition, said the company’s executive vice president of transportation and logistics, Kevin Ridings.
Clean Harbors utilizes a virtual private network that is accessible via laptops, but also has dispatchers working from office workstations who needed a method of accessing the system. Now, employees have their own iPhones, given by the company, which allow all workers to access the essential planning and dispatch database through iPhone applications.
Still, though, Sysco executive vice president and chief supply chain officer Marie Robinson believes remote working won’t last forever, and said some team members–especially management–will need to conduct employee evaluations or update engineering methods in person.
“This is the first time in my 32-year career when I’ve actually asked my associates to put themselves in a situation that I have not put myself in,” she said. “I want to get back into the truck.”
Reader Interactions