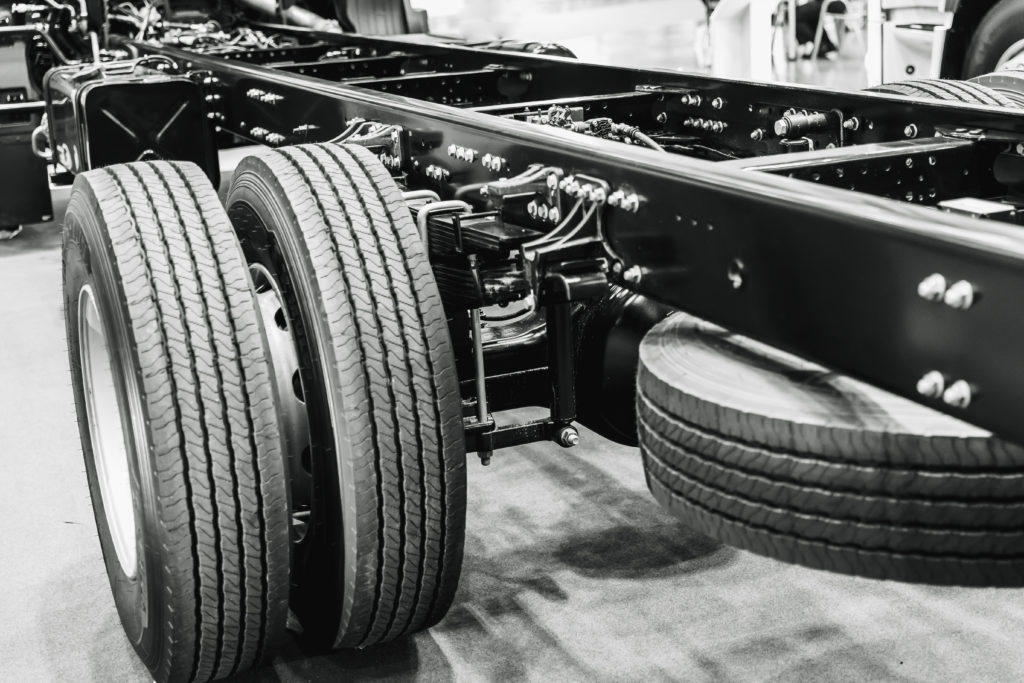
Fleets have been utilizing more technology than ever before in efforts to ensure drivers can conduct pre-trip and post-trip inspections properly and submit their findings ahead of schedule. Preventing roadside violations, maintenance issues, and vehicle downtime is vital in a fleet’s overall safety and efficiency.
Technology has also become extraordinarily helpful in boosting driver engagement and awareness during the inspection process.
“On a mechanical side, drivers need to be thorough on their pre- and post-trip [inspections] every single day,” said C.R. England Inc. Compliance Safety Accountability manager, Shana Hatch. “They need to be aware of how the equipment looks and feels and what they see [when] walking past.”
Drivers for C.R. England have a particular method of observing their trucks and making sure everything on their checklists is evaluated properly.
“I tell the drivers, everything on your pre-trip is the same as a Level II inspection, and the majority of violations found on a roadside inspection should have been noticed in a pre-trip if they’re doing a thorough pre-trip,” said Hatch. “Lights are either on or off. There is no in-between.”
For Boyle Transportation, the fleet uses a variety of methods to make sure inspections are done as efficiently as possible.
For example, it utilizes fleet management software Fleetio, which allows drivers to conduct inspections and submit their driver vehicle inspection reports right on the app.
“If [drivers] have a problem, they open the app, enter in what the issue is, and our maintenance department acts on it,” said Lasko, who noted that Fleetio has made communication easier than ever between drivers and maintenance workers.
Fleetio also keeps track of maintenance history for each truck and piece of equipment for truckers to have on file.
“You could then look [at the app] and say, ‘Mike reported two weeks ago [that] this trailer had low tread depth,’ so, right away, you know if there is something that needs attention,” Lasko explained.
Another method of inspection technology includes Zonar Systems’ Electronic Verified Inspection Reporting, which uses RFID and NFC tags on inspection zones throughout a vehicle, which drivers can scan during any inspection for further efficiency.
“Once they electronically sign the inspection, the results are uploaded into Zonar’s secure online portal and can be accessed by fleet managers,” said Zonar’s vice president of safety and compliance, Fred Fakkema.
These kinds of inspections have always been recorded manually and on paper, and sometimes those documents don’t make it to maintenance. Trimble Inc. transportation technology supplier said its technology circumvents that problem by integrating with an inspection’s DVIR process.
“The option of doing [pre- and post-trip inspections] or not doing [them] now that we’ve entered into the ELD (electronic logging device) phase has changed,” said Trimble’s senior solutions engineer, Dave Walters. “When the driver inspection is done, the data goes directly to the shop maintenance system. If there is a defect, the shop has to take some type of action.”
Walters noted that if a critical defect is indeed found, the shop will immediately begin taking action by sending out a vendor or bringing in a driver. If a defect found is noncritical, the system can track it and allow technicians to fix it the next time a truck enters the maintenance shop.
For Southeastern Freight Lines, DVIRs are utilized through Innovative Software Engineering (a company from Trimble), and stored there to comply with Department of Transportation guidelines. Southeastern’s telematics devices input DVIR, allowing drivers to see previous inspection reports and to sign off electronically.
“It also provides the driver the ability on the post-trip to document any issues that he experienced during this assigned scheduled run,” said Southeastern’s director of fleet services, Lee Long.
If any deficiencies are found, they are directly sent to Cetaris, Southeastern’s computerized maintenance software. There, all defects needing to be addressed are listed conveniently.
“It is all electronically handled,” said Long. “Our system provides work due reports that refresh routinely so we can see what has been requested for repair throughout the day.”
Then, requests made by shop, region, or by the entire system can be reviewed easily. The most common requests are “‘pulled in’ to a work order as being the primary reason for repair, and then a standard job is assigned to correct the defect and update the DVIR electronically,” Lee noted.
Reader Interactions