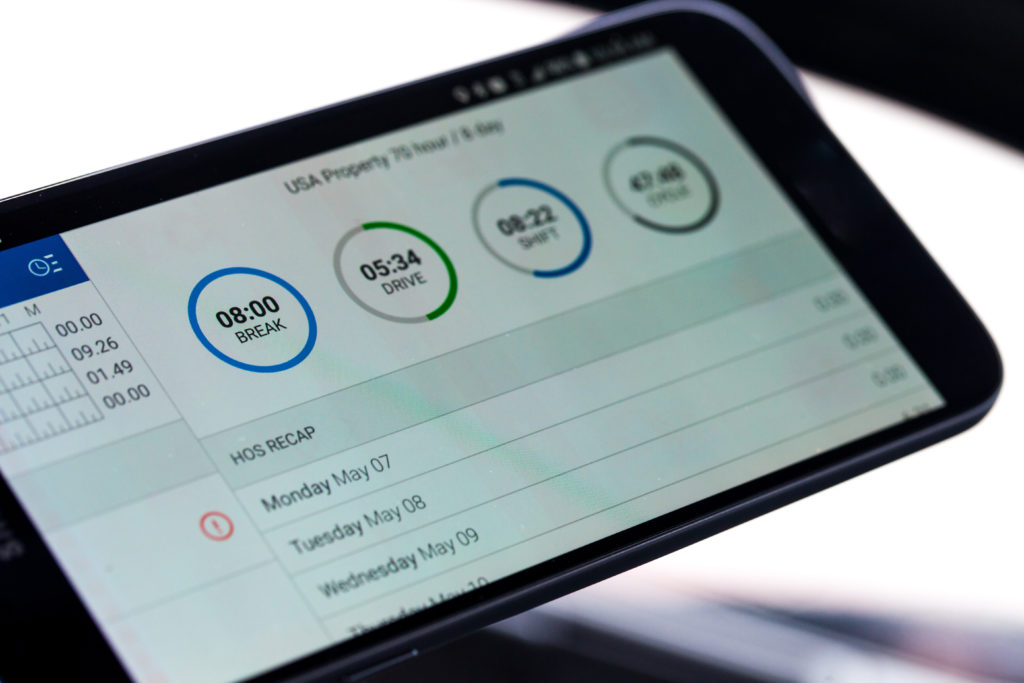
We recently reported on the effects of the latest ELD mandates on road safety and hours-of-service regulation compliance. But, how can ELDs also help fleets themselves better manage their businesses and employees?
“These devices help with understanding behaviors like speeding, hard braking, and over-accelerating,” said KeepTruckin vice president of product, Jai Ranganathan.
Dispatchers can even dispatch more quickly and efficiently with real-time location tracking through ELDs, which allows freight transportation to move as swiftly as possible.
“Dispatching has become the gold standard for efficiency, even in smaller fleets,” Ranganathan said.
“[ELD data] is straightforward and really leaves no room for interpretation, which is a good thing,” agreed Cargo Transporters vice president of safety, Shawn Brown, in regards to ELDs’ helpfulness with driver training.
Additionally, dispatching actions can also be improved by ELDs, explained vice president of product management at Trimble Transportation, Glenn Williams.
“By electronically capturing key hours-of-service data, fleets are also able to more readily pair available capacity with freight to reduce empty miles and backhauls, improve driver efficiency, and connect the entire supply chain to make it easier for shippers and carriers to work together,” he said, noting that supply chain transparency, vehicle utilization maximization, freight coverage boosts, and shipper-carrier communication have also seen major improvements with ELDs’ abilities to bring much higher levels of driver data access and vehicle connectivity to fleets.
ELD data can also help fleets lower overall detention time, fuel usage, and vehicle breakdowns by allowing them to better identify the best times at which certain vehicles can be properly dispatched, according to Michael Ahart, Omnitracs’ vice president of regulatory affairs.
“It can also be used to set realistic performance expectations with customers, allowing fleets to better predict arrival times based on HOS data,” he explained.
In fact, an overall decrease in delays has become a key focus in the use of ELDs, said director of operations at Grand Island Express, Deen Albert.
“It forced our driver managers to be very actively involved in the drivers’ hours, understanding where the drivers were, how much time they had left on the clock, and being able to maximize that,” he said.
For example, driver managers can track how long drivers are spending at home on their days off, explained Garner Trucking Inc. chief operating officer, Tim Chrulski.
“The data allows us, at a quick snapshot, to separate our data and look at hours,” he said. “Then, we track that weekly, so we’re fair and balanced for everyone.”
Fleets can also improve their overall route efficiency with ELDs, said Orbcomm’s director of fleet safety and compliance, Scott Stofer.
“They’re utilizing the system to the fullest to manage violations, manage fuel efficiencies, and make better decisions for dispatching,” he said.
J.J. Keller & Associates transport industry business adviser, Rick Malchow, added that fleets can track out-of-route miles and equipment-use efficiency with ELDs, as well as reduce shipper facility driver detention. If detention does occur, ELDs make it easier for drivers to get paid for that time.
Fuel consumption and vehicle idling tracking is also a helpful usage of ELDs, Ranganathan noted.
“This common-use case is helping to drive up the efficiency of trucks on the road while reducing carbon footprints across the country as more fleets utilize technology,” he said. “Data from ELDs helps eliminate the administrative burden of collecting state mileage and fuel receipts and automatically calculates this information instead.”
Driver education is another bonus of ELD implementation, said Cargo Transporters’ Brown.
“One big factor for a driver is trip planning and taking the time to think about not only your next stop, but the stop after that and where you’ll be parking for the next HOS break, etc.,” he explained. “Knowledge is power, and the ELDs provide much-needed real-time data that is very helpful in maximizing a compliant workday.”
ELDs may even be the launching-off point for further safety technology adoption, Orbcomm’s Stofer noted.
“In a lot of ways, the ELD mandate has accelerated the adoption not only from the provider side, but also from the carrier side,” he said.