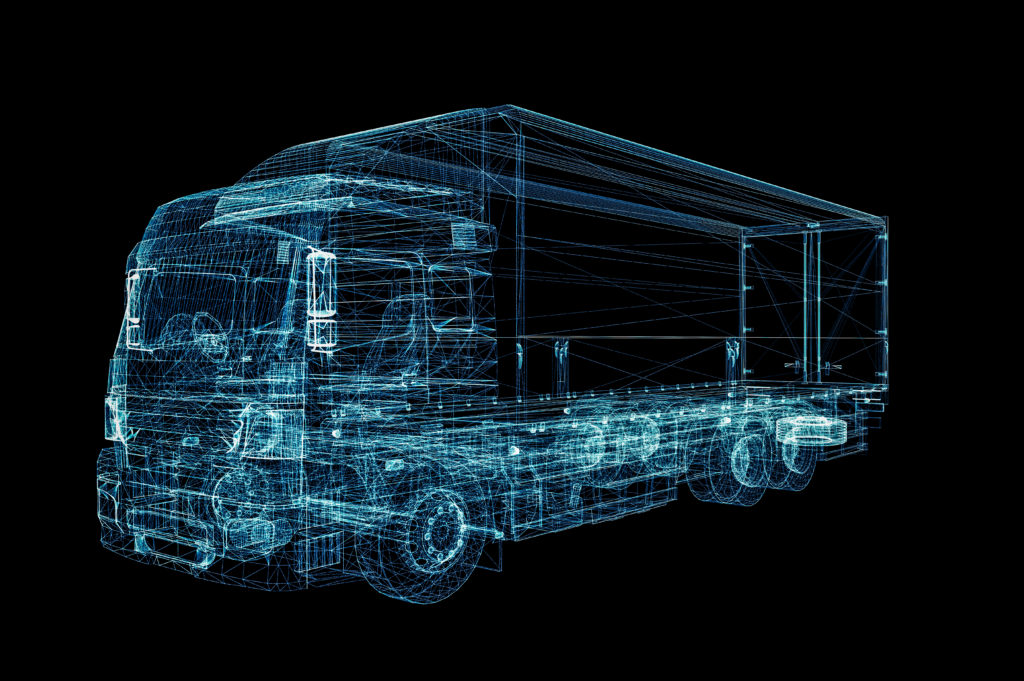
Kodiak Robotics, a self-driving truck company based out of San Francisco, has finally detailed its recent approach to the challenge of giving long-haul trucks self-driving technology after its 350th commercial delivery.
The company has released a 49-page safety self-assessment report demonstrating its commitment to public safety. The report gives a detailed explanation of how the startup operates and programs its autonomous vehicle technology.
“We believe it’s critical that we begin the process of explaining to the general public not just how we are safely testing our vehicles, but how we’re going to prove, mathematically and in plain English, that our vehicles are comprehensively safe even without a person behind the wheel,” said Kodiak co-founders Paz Eshel and Don Burnette.
This candid self-assessment aims to soothe any skepticism among the public and build trust and rapport with other motorists on the road.
“Given our progress, we think it’s time for Kodiak to start talking more about our unique, truck-focused technology,” said Burnette, who has previously worked for companies such as Otto, Uber, and Google.
Kodiak uses computer simulation and test track runs to examine and analyze its technology. The company was founded in April of 2018, had its first on-road test the following March, and made its very first delivery in July of 2019. Now, it has a fleet of 10 trucks hauling commercial freight throughout the state of Texas. Kodiak is also one of only a few trucking startups working to bring automation technology to long-haul trucking.
The startup’s technology often mimics how human drivers operate vehicles, such as within its ability to use lane markings as visual cues, rather than built-in map programming. This system within the “Kodiak Driver” allows for the vehicle to respond to and avoid unexpected obstacles on the road, like construction projects, even when the program’s maps don’t show them.
This ability is referred to as “perception over priors–i.e., that the Kodiak Driver trusts its eyes, not its memory, and we believe it represents a significant step forward for the AV industry,” said the company.
In its safety assessment, the Kodiak team shares its reasoning for focusing heavily on “structure highway driving” rather than city driving, as well as how its specifically-designed systems benefit heavy-duty trucks.
“We optimize our driving for safety, not comfort: paper towels don’t care if they get jostled a bit, whereas a rideshare passenger expects a smooth ride,” said the company.
In 2017, the National Highway Traffic Safety Administration released “Voluntary Guidance–Automated Driving Systems 2.0: A Vision for Safety,” which included a suggestion for any companies aligned with automated driving systems to provide a public assessment of their approaches to safety.
Since this recommendation, nearly two dozen companies have submitted these assessments, including other automated commercial vehicle competitors of Kodiak, like Waymo, TuSimple, and Starsky Robotics–although Starsky has since gone out of business.
“At Kodiak, we are strategic about every mile we drive,” said the company in its report. “We never drive our trucks for the sake of just logging more miles. Of course, this disciplined approach means we will probably never log as many test miles as some of our competitors. We see our lower mileage count not as a risk, but as a sign of our commitment to safety.”
Also present in Kodiak’s report was its explanation of its commercial-grade steering column “designed specifically for trucks,” which will eventually expand into dual-redundant electric motors that will allow the automated system to stay easily controlled if one motor fails. The system’s sensors also have “overlapping fields of view, so that every region around the truck is seen by multiple sensors,” which will allow the Kodiak Driver to always know the details of its surroundings, even if a sensor might fail. The AV technology will actuate the vehicle on “redundant, fault-tolerant computers,” that will run independently from the main computer. “These computers always know how to bring the truck to a safe stop, so that if the main computer should ever fail, they can safely achieve a Minimal Risk Condition,” the report stated.
Still, deploying a fleet of self-driving trucks without a safety driver on board is not likely to happen within the next year, Burnette explained.
“The fact is, once people get used to them, self-driving trucks will actually be pretty boring,” he said. “They’ll largely stay in the right lane, they’ll never weave in and out of traffic, and they’ll never speed.”
Supporters of automated vehicles within the commercial truck industry say these trucks will be much safer than human drivers, who often run red lights, text, fall asleep at the wheel, or otherwise become dangerously distracted while on the road.
“Our mission is to build the world’s most efficient, reliable, and respected freight carrier, using our autonomous technology,” explained Burnette. “Operating as a carrier will allow us to design our technology to meet shippers’ needs, and ultimately allow us to build a better product.”