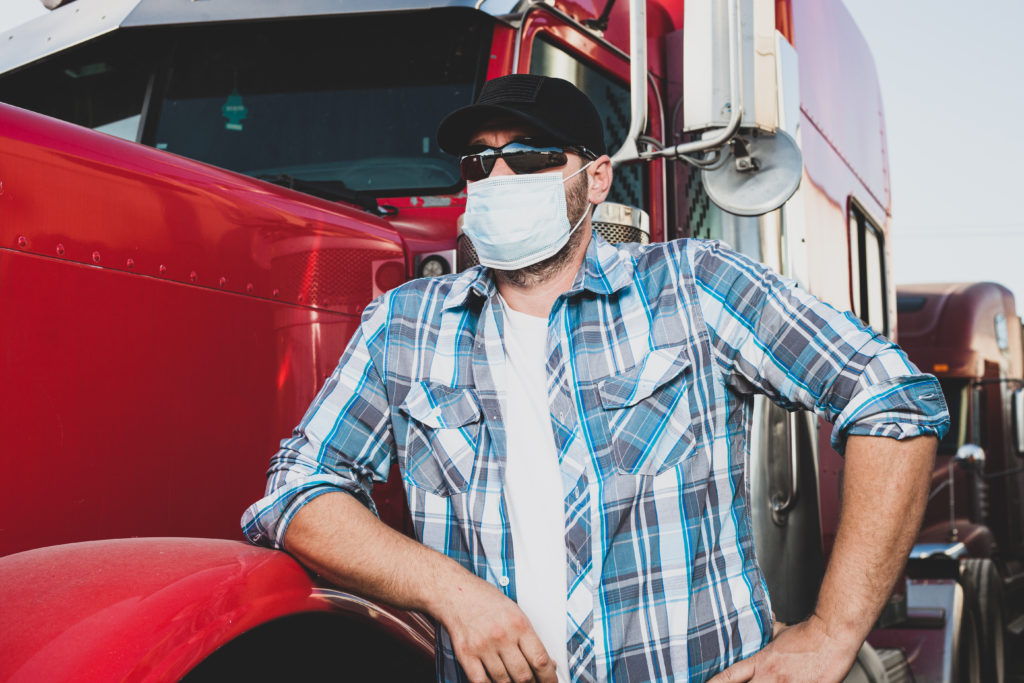
Some major commercial vehicle suppliers have taken on extra work in their already busier-than-normal schedules during this pandemic to help provide necessary materials and products for medical personnel across the country.
“There is no business model required for doing the right thing,” said James Sears, CEO of Sears Seating–one of the longest-operating trucking companies in the country.
The company has been making efforts towards a goal of making 3,000 medical gowns and 5,000 masks out of on-hand materials. Workers have been streamlining the production process of these items to be able to make around 200 gowns or 500 masks each day.
“Through the collaboration of Sears Seating’s engineers, expert sewers, and hospital staff, we are able to answer our community’s call for help. I could not be more proud of the team,” said Sears.
Sears Seating isn’t the only company reworking their production systems to help medical personnel. Toyota is also making various efforts to help reach “a recovery to normalcy as quickly as possible, and, in order to help that happen, [the company] is listening to the voices of many stakeholders to determine how it can contribute, with the aim to do what it can during this crisis,” the company said on its website.
Toyota has pledged to produce injection mold and 3D-printed medical face shields to help ease the current shortage. The company’s Teiho Plant in Japan said it will begin making at least 500 to 600 per week. Additionally, Toyota plans to use the Toyota Production System to help improve productivity in creating medical ventilators. The company is gathering a TPS support team that will be dispatched to companies currently struggling to increase medical equipment production.
Toyota also said it wild leverage its supply chain in an effort to produce hygienic products such as personal protective equipment, thermometers, face masks, and more, and that it would supply other equipment for the use of medical institutions, such as makeshift hospital beds, simple partition walls, and disinfectant containers.
Maumee, Ohio’s Dana Inc. is also working to use its supply chain and 3-D printers in order to create protective equipment open-source designs. Earlier in the pandemic, Dana worked with hospitals around Toledo to determine the best ways to design face shields and other protective gear.
“At Dana, we have a motto: People Finding a Better Way,” said Dana’s vice president of commercial vehicle drive and motion systems, Ryan Laskey. “But this is more than a motto–it truly illustrates our company culture. So, when our team heard of the shortage of personal protective equipment, they quickly went to work to find solutions.”
Dana is even working with local high schools, the University of Toledo, and Imagination Station to source material and efficiently produce face shields after the company prints the pieces for the shields in its Advanced Manufacturing Center 3-D Printers. Altogether, the company and its partners have been delivering at least 100 shields a day, and believes this number will increase as the designs become open-source.
This group has also created an intubation box which would create extra protection for hospital workers by partially enclosing a patient. So far, the team has delivered three dozen of these boxes to nearby hospitals. Additionally, Dana is utilizing its global supply network in further efforts to make glasses, glove, gown, shoe cover, and mask delivery a more streamlined process.
Additionally, Cummins Inc. has been donating its materials used for air, fuel, and lube filtration products made for heavy duty diesel engines to be used instead for N95 respirator masks.
The University of Minnesota created the mask prototypes with Cummins’ filtration materials, which uses DuPont’s hybrid membrane material, in a widespread effort to get more N95 masks to health care systems across Minneapolis.
“Since the arrival of the filtration media, we have been able to make rapid progress, and we now believe we have several viable mask options, including both a disposable and reusable option,” said University of Minnesota medical school dean Jakub Tolar. “These designs show real promise in keeping our health care workers safe should standard medical supplies of N95 masks no longer be available.”
Reader Interactions