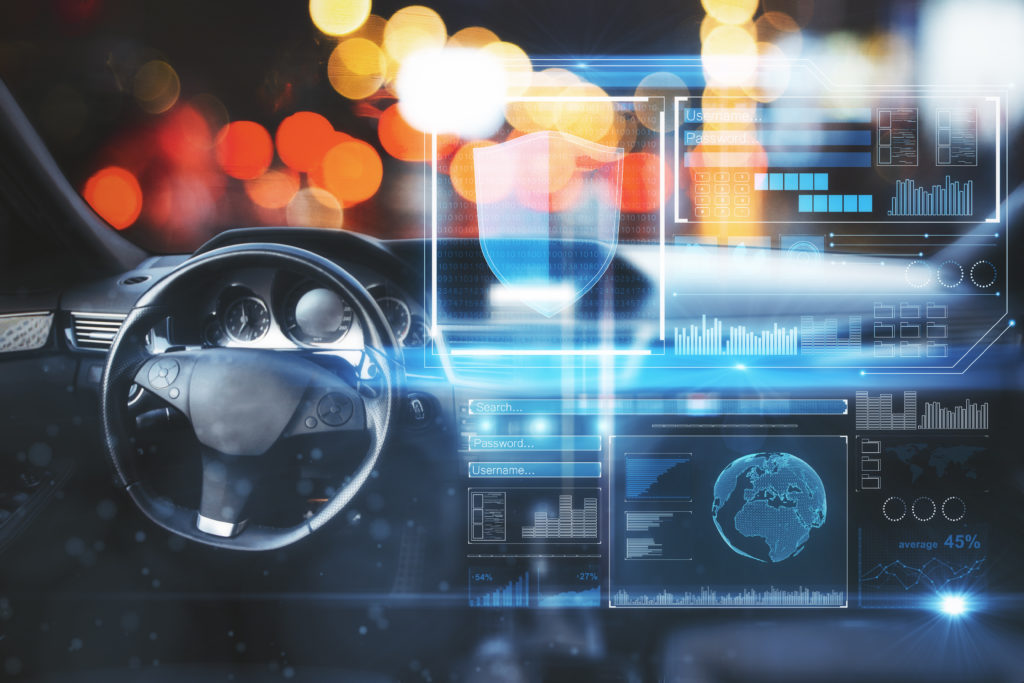
Although many companies within the trucking industry have been hit hard financially during the COVID-19 crisis, many have gained much clearer insight into the necessity of high-quality and innovative technology in regards to their day-to-day operations.
Throughout the pandemic, technology investments have varied based on American fleets’ freight sectors, as well as their need to keep employees working from home and adhere to their drivers’ necessary safety precautions.
For example, for Paper Transport, a company with a fleet of 900 tractors and 3,000 van trailers, COVID-19 “has accelerated our ongoing investment” in technology, according to the company’s organizational development manager, Julie Decker.
“Our corporate office staff has been remote since March. We expect much of our workforce to remain remote through summer.” Decker also said that Paper Tranport’s truck-based tablets have allowed for these changes to be as seamless as possible for its employees.
The company, which operates across multiple freight segments–with paper products being a major one–saw its freight voluming skyrocketing during the pandemic, as well.
“Toilet paper during panic buying was crazier than you would ever imagine,” said Decker. Because of this, Paper Transport accelerated its tech implementation, with help from Trimble Transportation.
“We have been active, early adopters of a few new software solutions provided by Trimble since last year, and each of those has launched in production during the pandemic.”
Ozark Motor Lines in Memphis had been working on implementing video telematics systems in all of its tractors since January, and is planning to continue the endeavor despite any financial setbacks. The company is installing Lytx units in 750 tractors, according to Ozark’s vice president of safety, Patrick Landreth.
Now, instead of needing to wait for drivers to be routed to an Ozark Motor Lines destination to receive safety coaching, the company can send a recording of an on-road event to the driver and then connect with the driver for coaching and counseling.
“When you consider the social distancing guidelines with the pandemic, that remote coaching is huge,” said Landreth.
Lytx’s vice president, Rob Abbott, reiterated the present need for telematics systems, saying for many carriers, this pandemic has “accelerated and exacerbated” the overall necessity.
“We’ve seen fleets accelerate implementation without first conducting a long test,” and relying heavily on other industry businesses’ recommendations, Abbott explained. Extensive testing for these technological systems was a typical precaution before the pandemic.
When Lytx visited Ozark Motor Lines to install units along with the carrier’s technicians, they realized the installation process would be similar across different model years.
“Our mechanics took it and ran,” said Landreth. “They have been getting multiple trucks done per week. We don’t think we’re going to have any trouble hitting our target date.”
This project also includes system installation on around 60 owner-operator trucks, with the vendor implementing units onto independent operators’ tractors of all makes and models.
For installers, drivers, and fleet workers, the majority of training must be virtual now, Abbott said. “Whereas before, we might prefer an in-person session with a group.” Lytx utilizes methods of training within web meetings, online teaching modules, and video training.
Many areas of the trucking industry have seen such a rise in demand that quick technology implementation is a must.
“The supermarkets are seeing a huge boom,” said Jonathan Bates, MiX Telematics‘ head of global marketing. “They’re having to lay on more drivers, more vehicles, more routes, and they need the visibility that telematics provides more than ever because the pressure is higher.”
Still, though, when the industry has seen slowdowns in the past, the effects have been different, said CEO of McLeod Software, Tom McLeod. He said this particular economic shutdown has shown trucking businesses where they need to be “more nimble and more able to withstand” any disruption.
“During an economic downturn, the larger companies tend to move ahead with their projects, because they’ve got a little more time to implement new systems.” he explained. For mid-market carriers, those businesses “tend to put the brakes on and wait to see when the economy’s going to pick up.”
McLeod has seen a huge boost in demand throughout the pandemic, and said other companies have also been “making a decision on much shorter time frames in order to address the need that’s been made obvious.”
He warned, though, that expediting automated business technology is not always wise.
“Sometimes I say, ‘With a computer, if you get in a hurry, it’s going to take longer,’” he explained. McLeod’s trucking software has “a very orderly and methodical process that we stick to because if you start trying to take shortcuts and skip steps, then sometimes you have a situation that needs to be cleaned up later.”
Reader Interactions