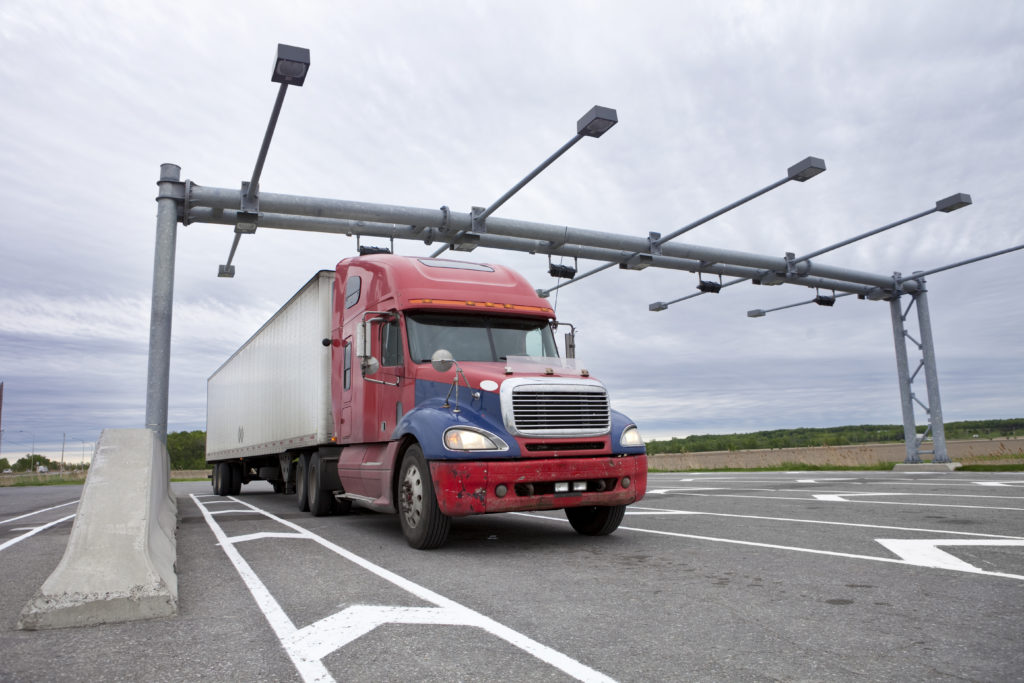
Like many events previously scheduled to take place this year, 2020’s International Roadcheck was postponed and rescheduled. The Commercial Vehicle Safety Alliance announced this month that the event, originally scheduled to take place in March, is now set for September 9th through the 11th.
“Although the coronavirus pandemic understandably shifted priorities and personnel during the spring, the commercial motor vehicle law enforcement community has reasserted its focus on the roadside inspection program and enforcement duties,” said Sgt. John Samis, President of CVSA. “Jurisdictions are nearly back to their pre-pandemic capacity with a strengthened concentration on identifying and removing unfit vehicles and drivers from our roadways using federal safety standards and the out-of-service criteria.”
The International Roadcheck has occurred right on schedule every year for the past 32 years, so the decision to postpone was “thoroughly and thoughtfully discussed,” Samis explained.
“This experience is unprecedented in our modern society, and we need to do all that we can to help stop the spread of this global pandemic,” he said at the time of postponement.
2020’s Roadcheck will be a 72-hour, boosted effort focusing on the category of driver requirements. CVSA-certified inspectors across North America will conduct visibility inspection and enforcement efforts including motor vehicle and driver inspections at weigh-in stops or inspection stations, which may be part of roving mobile patrols or specific fixed locations.
Throughout the three-day event, commercial motor vehicles will be thoroughly checked for federal regulation compliance, and law enforcement personnel will inspect for any item violations with the North American Standard Out-of-Service Criteria.
“As we urgently respond to this time-sensitive crisis, we must remain diligent and committed to ensuring that the commercial motor vehicles and drivers providing essential goods and services to our communities are following motor carrier safety regulations,” said Samis. “Safety doesn’t take a break. It is always our top priority.”
Inspectors will collect and verify a driver’s documents during the driver portion of the inspection. They will be careful to accurately identify the motor carrier, check records-of-duty status, examine the driver’s license, and check periodic inspection reports. If needed, the inspector will also check the Medical Examiner’s Certificate, the driver’s daily vehicle inspection report, and the Skill Performance Evaluation Certificate.
Drivers will also be checked for illness, fatigue, proper seat belt usage, and any drug or alcohol possession or impairment.
Any commercial motor vehicle drivers operating without all necessary credentials, driving while ill, fatigued, or otherwise impaired, in violation of any hours-of-service rules, or under the influence of or possessing any drugs or alcohol could be placed out of service.
When placed into an out-of-service status by an inspector, the vehicle will become restricted from any travel until all violations are corrected.
The inspection portion for vehicles include thorough checks of: brake systems, cargo security, coupling devices, drive-line components, drive-shaft components, presence of the driver’s seat, exhaust systems, frames, fuel systems, lighting devices, steering mechanisms, suspensions, tires, van and open-top trailer bodies, wheels, rims, hubs, and windshield wipers.
All American commercial motor vehicle inspections are an effort to check for compliance with the Federal Motor Carrier Safety Regulations. Canadian standards are based on many provincial and territorial mandates along with the National Safety Code, and Mexican commercial motor vehicles are checked for compliance with Normas Oficiales Mexicanas standards.
Inspectors will typically perform the North American Standard Level I Inspection during an International Roadcheck. This inspection consists of 37 steps within two main categories, along with a driver operating requirements and vehicle mechanical fitness examination. Hazardous materials and dangerous goods may also be a third category component of a Level I Inspection, if needed.
CVSA’s International Roadcheck partners with the Federal Motor Carrier Safety Administration, the Canadian Council of Motor Transport Administrators, Transport Canada, and the Ministry of Communications and Transportation of Mexico.
The International Roadcheck gives particular emphasis to one specific category of violations each year. This year’s focus on driver requirements comes after FMCSA’s data from last year’s Roadcheck showed that out of approximately 3.36 million inspections, 952,938 driver violations were found, and 199,722 of those were out-of-service conditions.